4 Most Popular Branding Options in Eyewear Industry
We are going to discuss common LOGO printing technology for eyewear frames, this article explores each technique in detail, highlighting their applications and benefits in modern manufacturing and branding
In the competitive world of branding and product customization, high-quality logo printing plays a crucial role in enhancing eyewear brand's identity and product appeal. Various advanced printing technologies are widely used to achieve durable, precise, and visually striking logos on different materials.
Among the most common techniques are Screen Printing, Laser Engraving, UV Curing Lamination Technology, and Hot Foil Stamping, each offering unique advantages depending on the application requirements.
Logo Printing Technics
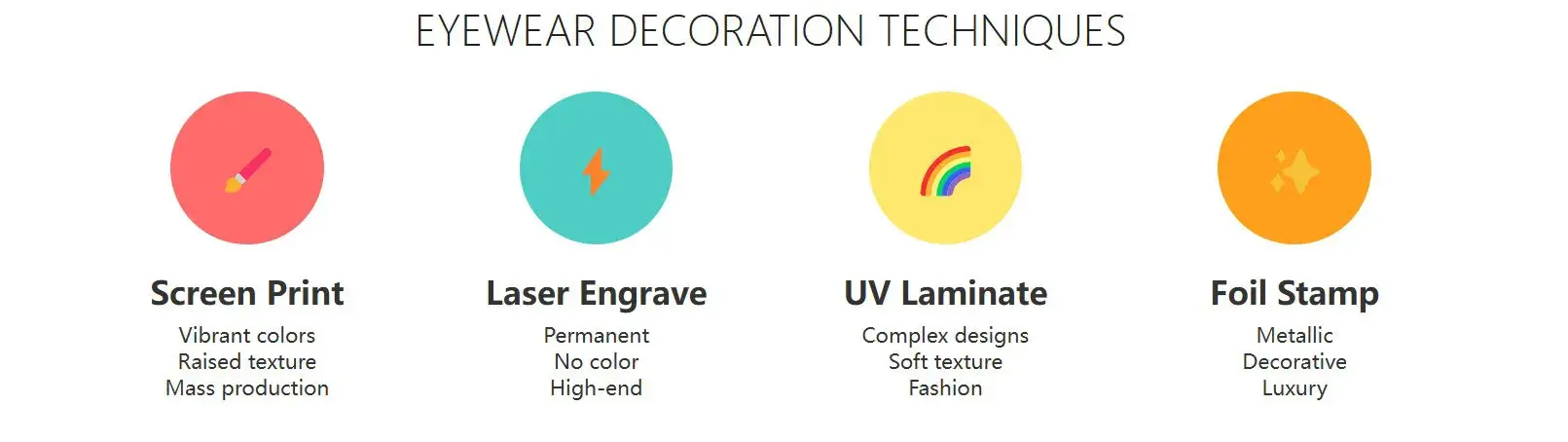
1.Screen Printing
Screen printing involves the ink being squeezed through the mesh openings of the screen plate by a squeegee, adhering to the surface of the temple, and then cured in an infrared tunnel oven (drying temperature: 60-80°C).
Manual machines are suitable for small-batch customization, with an efficiency of 50-100 prints/hour. They rely entirely on manual alignment and ink scraping, making them ideal for low-volume production. Semi-automatic machines, suited for small to medium batches, achieve 200-500 prints/hour.
Eyewear manual screen printing machine's advantage lies in machine-assisted positioning and ink scraping, significantly reducing human error. Fully automatic machines feature automated feeding, positioning, printing, and drying, with a printing efficiency of 800-2,000 prints/hour, making them ideal for large-scale production.
Additional costs include screen plates (€6-38/plate), ink (€12-63/kg), and labor costs for 1-2 operators. In the eyewear industry, semi-automatic and fully automatic machines are more commonly adopted due to their higher production efficiency, which is one of the reasons why higher order quantities lead to lower per-unit costs.
2. Laser Engraving
Laser engraving is a prevalent technique for applying logos on eyeglass temples. The process utilizes high-energy laser beams to physically ablate metal or plastic surfaces, creating permanent recessed markings through controlled power and path modulation.
The technology's paramount advantage lies in its permanence - direct material ablation ensures logos remain legible despite prolonged wear or friction, eliminating fading or peeling risks. Visual outcomes are material-dependent: metals yield matte silver finishes, while plastics may require pigment infill (e.g., black) for contrast enhancement.
Though requiring substantial initial investment, laser systems deliver superior production efficiency, resulting in exceptionally low per-unit costs at scale. The engraved textures exhibit refined tactile quality with dimensional depth, offering enhanced detail resolution that aligns with premium eyewear branding requirements. This combination of durability and precision makes laser engraving particularly suitable for mid-to-high-end market segments.
3.UV Curing Lamination Technology,crystal glue
UV Curing Lamination Technology is primarily employed for manufacturing high-quality lens or frame coating products. This process enhances production efficiency while maintaining precision and consistency, making it particularly suitable for small-to-medium eyewear manufacturers.
The semi-automatic UP film system utilizes precision mechanical structures and control systems. Key modules include loading, positioning, adhesive dispensing, lamination, and curing. Operators place components on dedicated fixtures, with vision/mechanical alignment ensuring ±0.1mm accuracy before automated adhesive application and film bonding.UV or hot-melt adhesives are precisely dispensed via metering systems to prevent bubbles or overflow.
This process achieves an optimal balance between cost, efficiency and quality, ideal for high-mix, low-volume production while maintaining competitiveness in demanding markets.
4.Hot Foil Stamping
Hot Foil stamping in the eyewear industry is a widely used surface decoration technique for frames and temples, transferring patterns, text, or metallic effects onto substrates through heat and pressure. The process relies on precisely controlled temperature (120–200°C), pressure (0.2–0.8MPa), and dwell time (0.5–3 seconds) to bond the decorative layer from the stamping foil to metal, plastic, or composite frames.
Luxury brands combine it with plating for dual-tone effects. Eco-friendly advancements include water-based adhesives and biodegradable foils (15–20% cost premium), complying with REACH standards. Balancing cost efficiency, design versatility, and durability, hot Foil stamping remains a key finishing solution in eyewear manufacturing.
Effect characteristics and differences
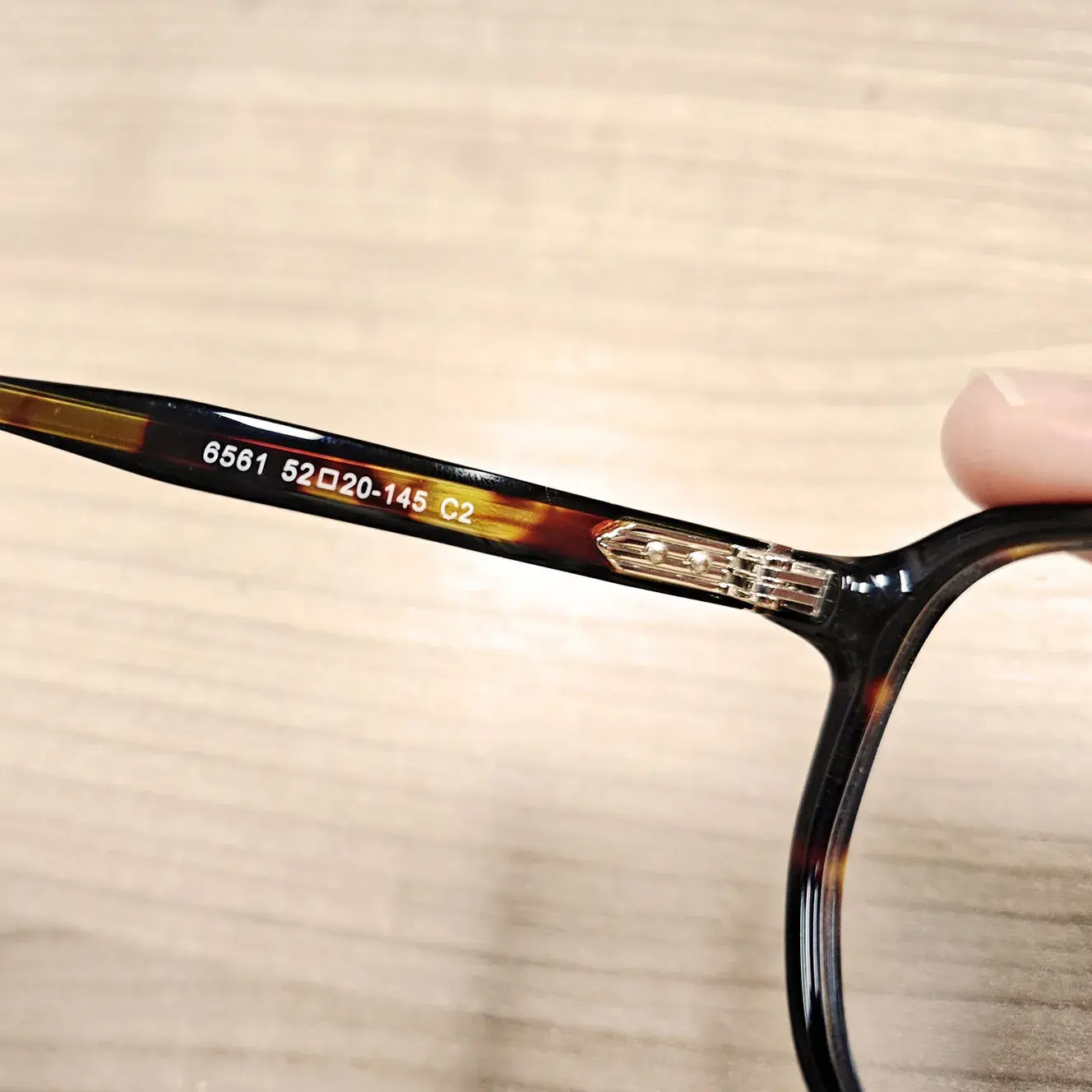
1. Screen Printing
Color Saturation:
High, capable of vibrant and solid colors, ideal for simple gradients or flat designs.
Texture:
Slightly raised surface with a smooth touch, though uneven ink thickness may cause graininess.
Fading/Peeling:
rolonged friction or chemical cleaning may cause wear, but high-quality UV-cured inks offer better durability.
Materials:
Metal, plastic, acetate, and flat/curved surfaces (with special treatment).
Applications:
Mass production, suitable for classic or fashion eyewear with solid-color logos.
Limitations:
Limited capability for complex gradients or high-resolution details; high cost for small batches.
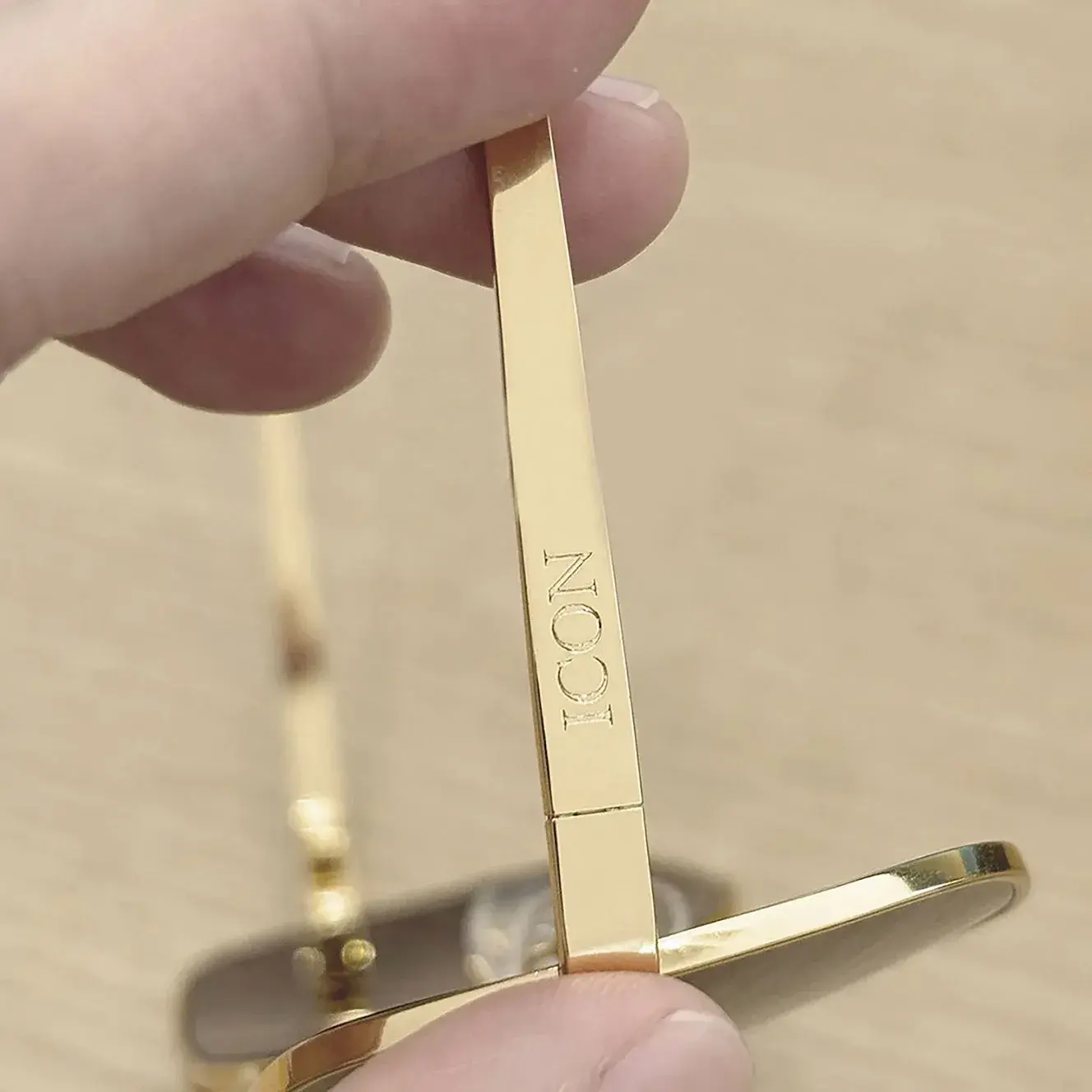
2. Laser Engraving
Color Saturation:
No color—relies on material’s natural tone (e.g., gray/black on metal, internal engraving on transparent materials).
Texture:
Tactile recessed or raised engraving; metal surfaces may feel slightly rough.
Fading/Peeling:
Permanent, no fading or peeling (unless the material surface is damaged).
Materials:
Metal (titanium, stainless steel), acetate, certain plastics.
Applications:
High-end custom or business eyewear, emphasizing durability or minimalist design.
Limitations:
Cannot achieve color; dark materials may require shallow engraving for contrast.
3. UV Curing Lamination Technology
Color Saturation:
Vibrant, customizable patterns (e.g., gradients, wood grain, carbon fiber).
Texture:
Soft, elastic texture resembling leather or rubber.
Fading/Peeling:
UV-cured inks are scratch-resistant, but prolonged sun exposure may cause slight fading; adhesion outperforms screen printing.
Materials:
Moderate abrasion resistance; edges may peel under repeated flexing or sharp impacts.Water-resistant but may fade under prolonged UV exposure.
Applications:
Used for full or partial coverage on fashion/sports frames. Best for designs requiring soft textures and complex graphics.
Limitations:
Edge wear over time, higher cost than foil stamping.
4.Hot Foil Stamping
Color Saturation:
Metallic finishes (e.g., gold, silver) or high-saturation colors, limited by foil material options.
Texture:
Smooth and rigid surface with pronounced reflective gloss.
Fading/Peeling:
Prone to abrasion and delamination, especially at edges.Susceptible to solvent/heat exposure, leading to fading over time.
Applications:
Ideal for logos, text, or decorative accents on high-end frames. Suitable for metal or acetate frames; not recommended for full-surface coverage.
Limitations:
Limited design flexibility (only for flat/simple curved surfaces).
the choice of logo printing technology depends on factors like material, durability, and budget. Screen printing offers vibrant colors and cost-effectiveness for bulk orders, while laser engraving provides precision and permanence on metals or wood. UV curing lamination ensures high-gloss finishes and scratch resistance, ideal for premium products. Hot foil stamping delivers elegant metallic or matte effects for luxury branding. Each method has unique advantages, allowing businesses to tailor their logo presentation to enhance brand identity. By selecting the right technique, companies can achieve professional, long-lasting results that align with their aesthetic and functional requirements, ensuring impactful visual communication across various applications.